Why Does NTM Have Lead Times on its Gutter and Roof Panel Machines?
At New Tech Machinery (NTM), we’re often asked why lead times for our roof panel machines can run up to 22 weeks, and three weeks for gutter machines. One factor has to do with the high demand for portable rollformers given the growing metal construction industry. As happens in the market, demand can exceed supply. Also, supply-chain issues can play a role, as our raw materials come from all over the world. However, another less talked about reason is what goes into making each machine, as NTM rollformers are not manufactured on an assembly line. From frame building to final product, nearly every part is made, installed, and inspected by our machine specialists.
While this article will give you an understanding of our lead time, it will also show you how NTM machines are produced so that you can be a better-informed owner and know in detail how your machine is put together.
In this article, we’ll cover:
- NTM’s two manufacturing plants
- The machine stations in each plant
- The assembly and adjustment processes
- Inspection and testing
NTM Plant, Hermosillo, Mexico
The first manufacturing point for the NTM SSR™ MultiPro Jr. Roof Panel Machine, the SSH™ MultiPro Roof Panel Machine, the SSQ II™ MultiPro Roof and Wall Panel Machine, and the Mach II™ 5″, 6″, and 5″/6″ Combo Gutter Machines is in Hermosillo, Mexico. There, parts are manufactured, and basic machine assembly takes place.
A 27,000 sq. ft. plant, Hermosillo includes the following stations:
- Welding
- Panel assembly
- CNC lathes and mills
- Roller set manufacturing
- Gutter machine assembly
- Accessories assembly
Welding Station
The frames are welded together at the welding station, which is the first step in the process of producing an NTM portable rollformer. All parts of the frame, including the shear mounting blocks, motor mounts, tensioner mounts, and exit side mounting tabs, must be set exactly so as to align with the other parts of the machine to be installed later. Bottom drive roller subassemblies are tapped until flush with the frame. The squareness of the frame is measured to check symmetry before the subassemblies are welded.
The manufacturing of the frame is an essential piece of the machine-building process, much like laying the foundation of a house upon which everything else is built. It must be solid and perfectly balanced.
Other parts welded include hydraulic tanks and accessories like run-out tables and de-coiler stands.
Panel Assembly Station
The assembly that takes place for the SSQ II consists of the frame, drive rollers, and width adjustment. The SSR MultiPro includes the shear as well. The SSH MultiPro includes only the frame.
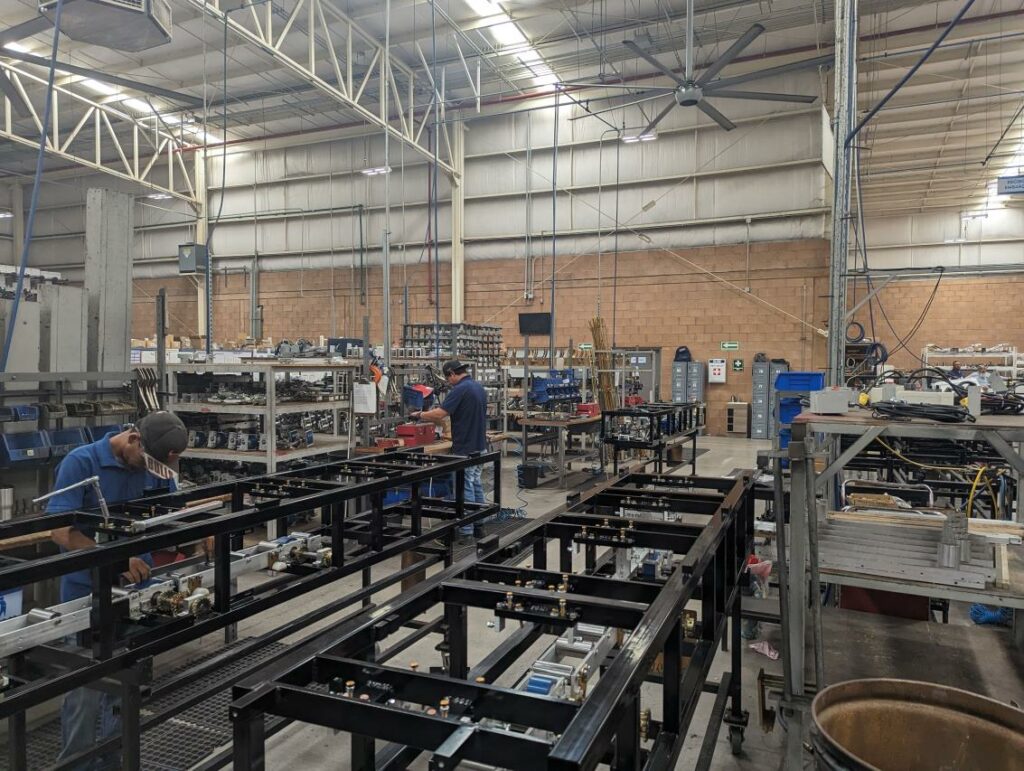
Lathes and Mills
There are nine CNC lathes and nine CNC mills, which form nearly all of the internal machine parts. This includes rollers and shafts. The machines run nearly constantly over two shifts per day.
All parts manufactured in Mexico, like the shears, form rollers, reel racks, and hydraulic tanks, are shipped separately to be assembled into the machine at the NTM plant in Colorado.
Roller Set Station
Roller sets, including those ordered as added options, are manufactured in Hermosillo, where they are assembled and adjusted. Rollers are buffed, aligned, and correctly spaced, then carefully packed for shipment. They undergo further testing and adjustment at the NTM plant in Colorado.
Gutter Machine Station
The Mach II gutter machines are built almost entirely at our facility in Hermosillo. Rails, rollers, shears, shear blades, box assemblies, entry guides, etc. are installed in this station. The covers, manufactured in the U.S., are added in Colorado.
Accessories Assembly Station
All accessories are manufactured and assembled at the Hermosillo facility. These include coil cradles, reels, arbors, and notching assemblies. The accessories are then packed for shipping where they will be stocked as inventory at the Aurora facility.
NTM Plant, Aurora, Colorado
Once the machine frames and components arrive at the NTM plant in Aurora, Colorado, they continue through the following stations:
- Panel Machine Assembly
- Adjusting
- Covering
- Finished Goods
- Gutter
- Shipping
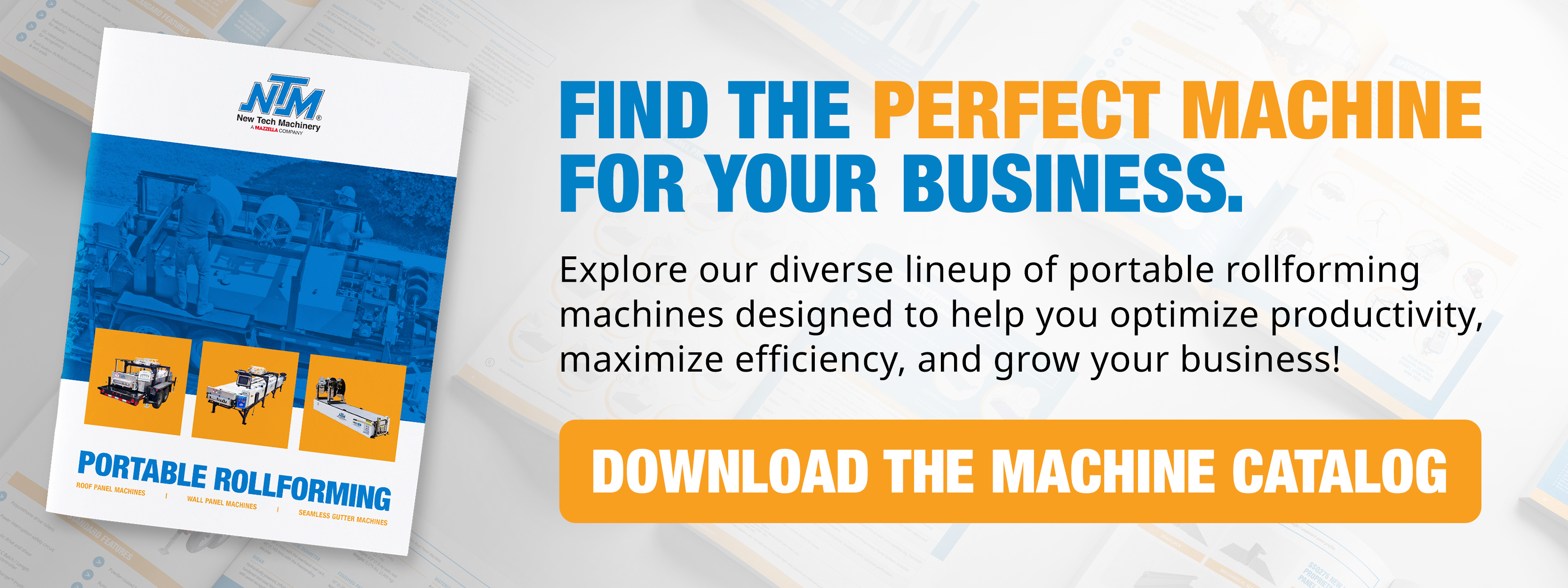
Panel Machine Assembly
After arriving from Mexico, the SSQ, SSH, and SSR machines start at the panel machine assembly area, which is made up of six work stations.
At these stations, NTM machinists do the following:
- Shimmy rails
- Roll over guide rods to shimmy both sides
- Adjust drives to strings
- Check side-to-side line up to string
- Measure with a measuring tape from the guide to the rod to string—25 ½” and 25” for each end
Once these adjustments have been checked, the next steps at this station include:
- Installing the shear
- Installing the entry guide
- Installing hydraulic tank and fluid connection hoses
- Installing the electrical and control panel
- Connecting the control panel to the electrical
The Panel Machine Assembly items are complete, clocked, and signed into the log, which then gets entered into the system for the machine’s records before moving to the next station.
Adjusting Station
The rollers are adjusted at this station to ensure the panels run through correctly. Hydraulics are run for the first time to check for leaks and other issues and adjusted as needed. The customer’s roller set is installed and then checked to make sure it was built to standards. The machine is then set to specifications, and the machinist runs panels, then straightens and adjusts accordingly until the panels run without flaw. All controller functions, for both manual and automatic controllers, are checked.
At the adjusting station, the following are added:
- Rib roller frame
- Roller set
- Rib Rollers
- Shear blades
- Shear dies
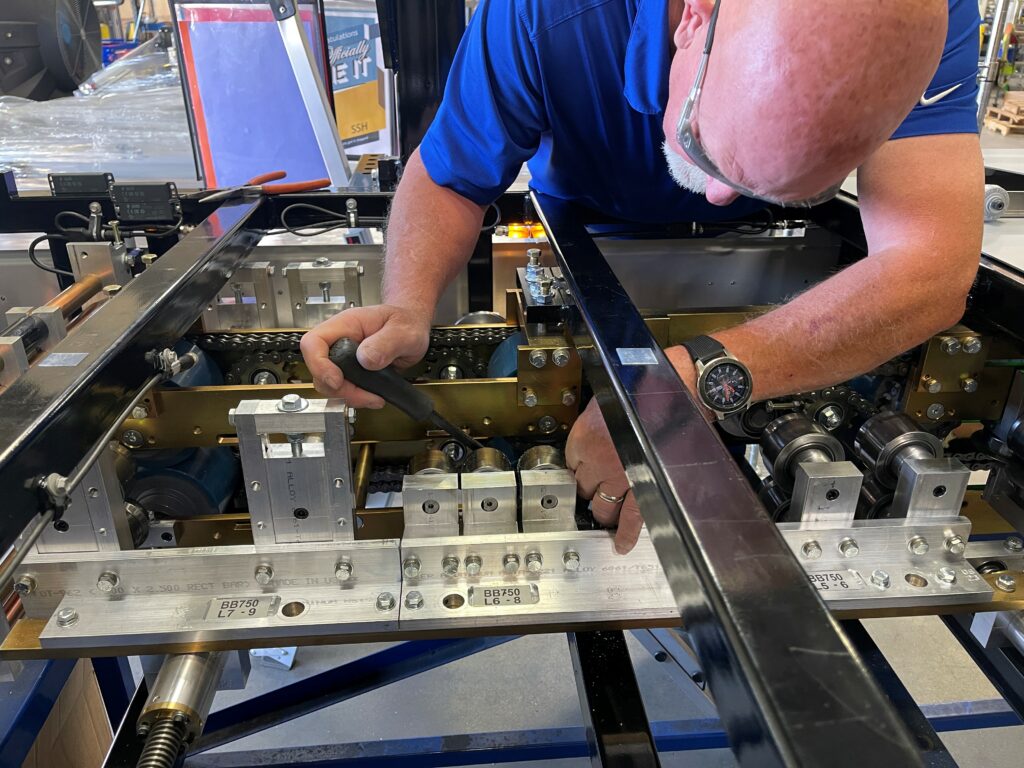
Cover Station
Before moving to the cover station, the machine undergoes a preliminary inspection. At the cover station, aluminum or steel covers are added, along with safety decals. Fine details get careful attention, including closing any gaps, smoothing rough edges, and tightening bolts one last time. The covers are given a final polish.
At the cover station, the following are added:
- Entry drum rollers
- Sensors
- Covers
The inspection takes place at the cover station by our machine inspectors using a thorough checklist. During inspection, the following takes place:
- Inspection of all bolts, parts, safety mechanisms, sensors, and labels
- Inspection of hydraulic pressure and machine functionality
The machine is operated, and materials are run through to test for performance.
Finished Goods Station
At this station, the machine is configured with accessories according to the customer’s order.
Testing Area
Before shipping, the customer’s machine receives its final test. The inspectors operate the machine as the owner or operator will, by running panels. They check the panels carefully to make sure they are producing free of defects. They also operate the controller and recheck all functions.
In the final phase, shipping, the machine is placed on a trailer or platform and wrapped.
All other external accessories, like additional profiles, must be checked and boxed for shipping.
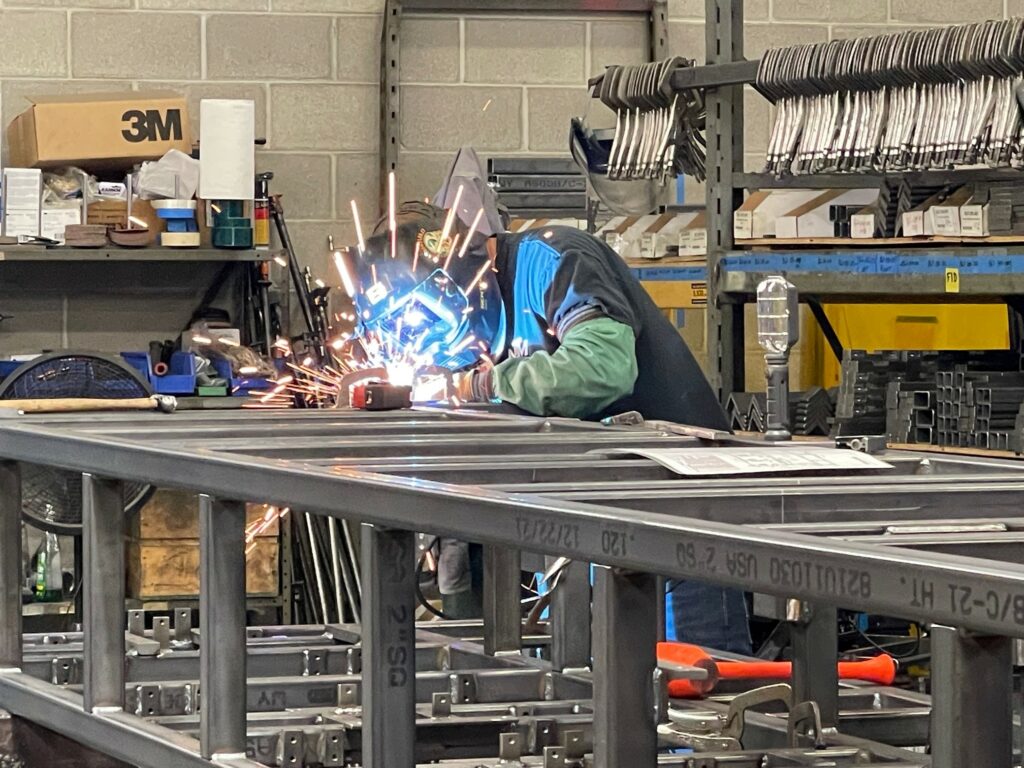
Gutter Station
The gutter machines arrive 95% complete from our Hermosillo plant. At the Aurora facility, machine specialists clean all parts with acetone to remove oils from parts that come into contact with materials, then follow a rigorous checklist that includes checking rollers, drives, and bearings; measuring alignments and gaps, and making adjustments to any parts. Machine specialists run materials through the machine for testing and set the machine according to the gauge of material the customer is likely to use.
Once the gutter machine has been tested, it’s equipped with its accessories and packaged for shipping.
Specialty Machines
The process for specialty machines does not begin in Mexico, as the machines are built from the frames up at the Aurora plant. These include the WAV™ Wall Panel Machine, 5VC-5V™ Crimp Roof Panel Machine, and the BG7™ Box Gutter Machine. The process starts at the welding station where the frames are put together. Three CNC lathes and a CNC mill mold the components, and from there, once the basic frames and drive rollers are assembled, they go through a similar process as the machines arriving from Mexico.
Final Thoughts on Lead Time
The SSR, SSH, and SSQ II lead times are currently between 20-22 weeks, and that isn’t expected to change much in the coming year. While the Hermosillo plant has broken ground on a new, larger building to be opened next year, the Aurora plant is at its limit for capacity. At 30,000 sq. ft., there isn’t room for expansion. While that eventually may change, for 2024 expect the same lead times. Gutter machine lead time is at about three weeks. Check the NTM website for lead-time updates.
For any questions or to find out more about our machines, please reach out to one of our account managers who can provide you with information about all of our machines and accessories.
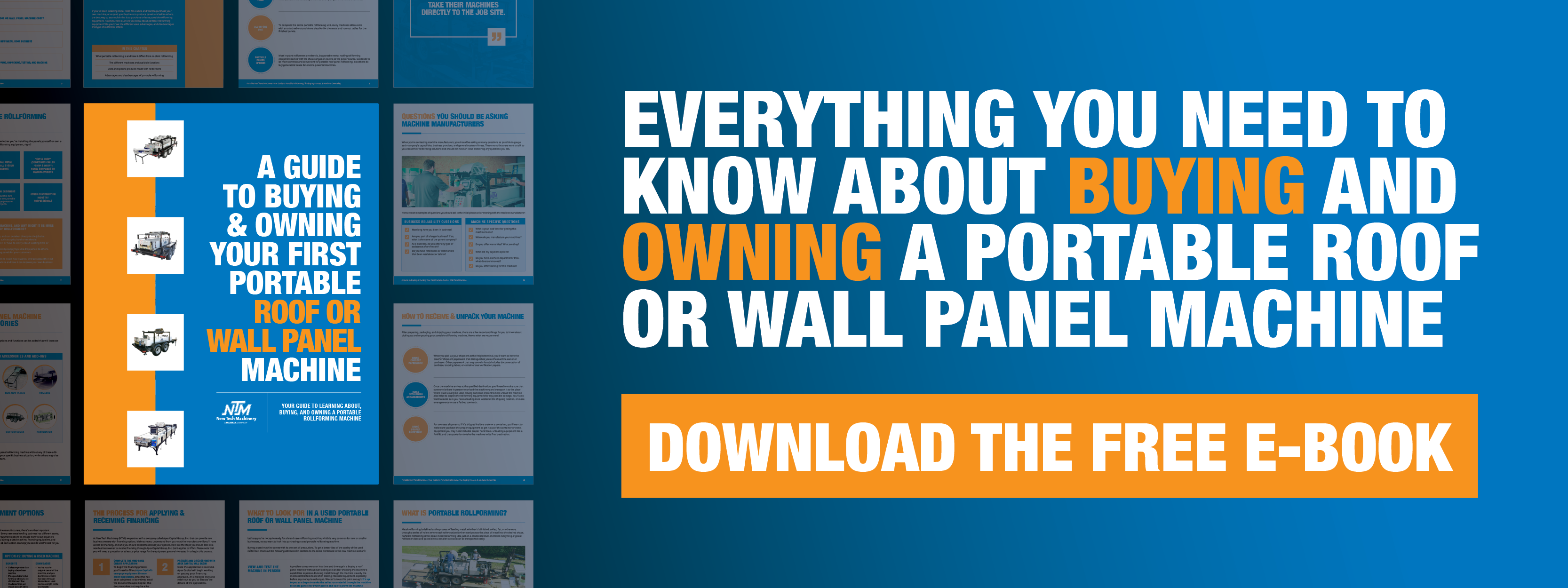