Problems with NTM Rollformers: Four Common Misconceptions
Have your heard about issues with New Tech Machinery (NTM) rollformers? Actually, we have. In fact, some problems we hear about often turn out to be common misconceptions that spread to other contractors. Kind of like the old classroom game where a message is whispered to one student, then gets passed down. The communication is usually completely different by the time it reaches the last one. So, while many metal roofing business owners are familiar with NTM’s machines, not everything they’ve heard about them is accurate.
New Tech Machinery has been helping metal rollforming contractors succeed for over three decades. We pride ourselves on listening to customer feedback so that our machines perform beyond your expectations.
In this article, you will learn about four common misconceptions about NTM MultiPro Roof Panel Machines so that you can be a more informed buyer:
- The post-cut shear on the NTM rollformer isn’t as good as the pre-cut shear.
- The overhead expandable arbor could drop into the machine while loading coil, causing damage.
- The drive chains stretch on NTM machines.
- Profile changeovers are difficult compared to cassettes that some other machines use.
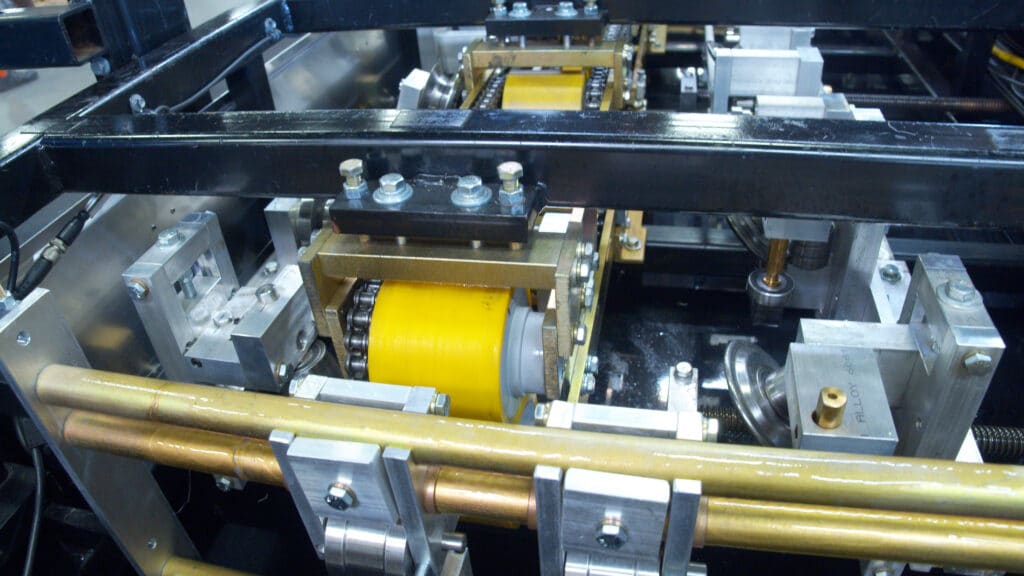
Problem 1: Pre-Cut vs. Post-Cut Shears
Pre-Cut Shears
A pre-cut machine cuts at the entry end, once the coil has run the specified length through the machine. A post-cut waits until the coil has run the specified length out of the machine, then makes the cut at the exit point.
There are advantages to both cutting from the entry and cutting from the exit points. Pre-cut shears provide a clean cut, allowing operators to hand-feed coil for low-volume production. Also, pre-cut shears require less maintenance. You don’t have to worry about changing dies with different profiles because cutting happens at the entry end, before the panel is formed.
However, some panels, like high-strength and heavy gauge steels, run better on post-cut shears. Also, some shorter panels, say for soffits, can’t be run with pre-cut shears, whereas post-cut can handle as short as 3″ or 4″ panels.
Pre-cut machines can also produce end-flare, which distorts the shape of the panel at the cut end, or at any section where a cut is made, making for tougher installation. Whereas post-cut shears are built into the machine, pre-cut shears require an external accessory and therefore add length to the machine, making it less ideal for portability.
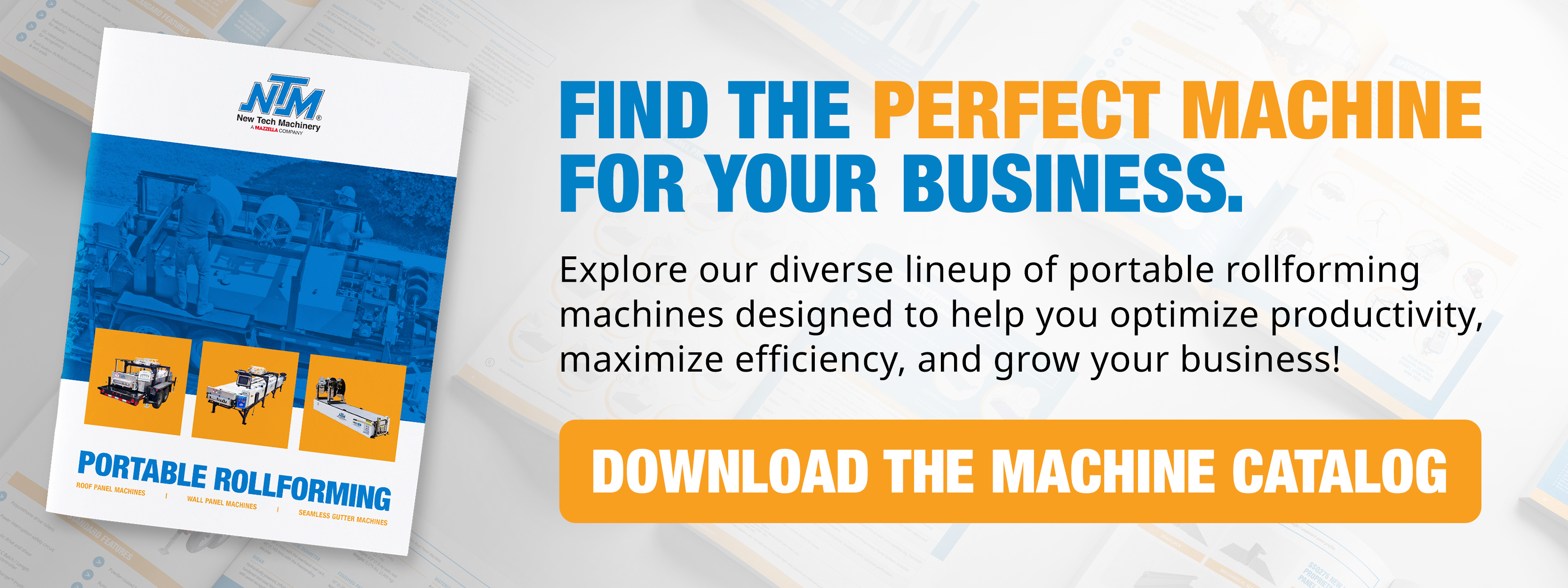
Post-Cut Shears
The main disadvantage to a post-cut shear is the high maintenance. The shear blade, as mentioned, needs constant lubrication. Then there’s the expense and maintenance of profile shear dies that need to be changed out with different profiles.
While the post-cut end may look a bit rougher frequent shear blade lubrication will greatly reduce this, and it’s worth noting that the edge gets tucked under, so it’s not really an issue. Plus, while the pre-cut may provide a cleaner cut, it isn’t ideal for every situation, including those already mentioned. Therefore, many contractors prefer the post-cut.
Some NTM users claim that the post-cut shear prevents oil canning because the drive and forming rollers are separate, so the material is continually being run through the machine. The form rollers and drive system automatically synchronize, preventing uneven speeds and friction, thus no oil canning. Also, there’s less tooling wear with the post-cut shear system.
For maintenance, we recommend lubricating the shear every 20 cuts or so. The pre-cut shear may not dull as easily as it’s cutting flat rather than formed material, but it also depends on the gauge and type of material you’re running. .032” aluminum will have much less impact on the shear than .22-gauge steel. As mentioned earlier, pre-cut does not do well with high-gauge and stronger metals.
It’s worth mentioning the proximity sensor on the exit end of the SSQ II MultiPro Roof and Wall Panel Machine and the SSH MultiPro Roof Panel Machine. The proximity sensor pauses machine operation if a panel hasn’t been removed once it moves past the shear. This way, the panel isn’t damaged or scratched by being pushed out, as the machine will run at the operator’s pace. Once the panel has been removed, the machine will resume the sequence. The SSQ II and SSH are the only machines on the market that offer this feature. Next, we’ll explore your options for holding the coil.
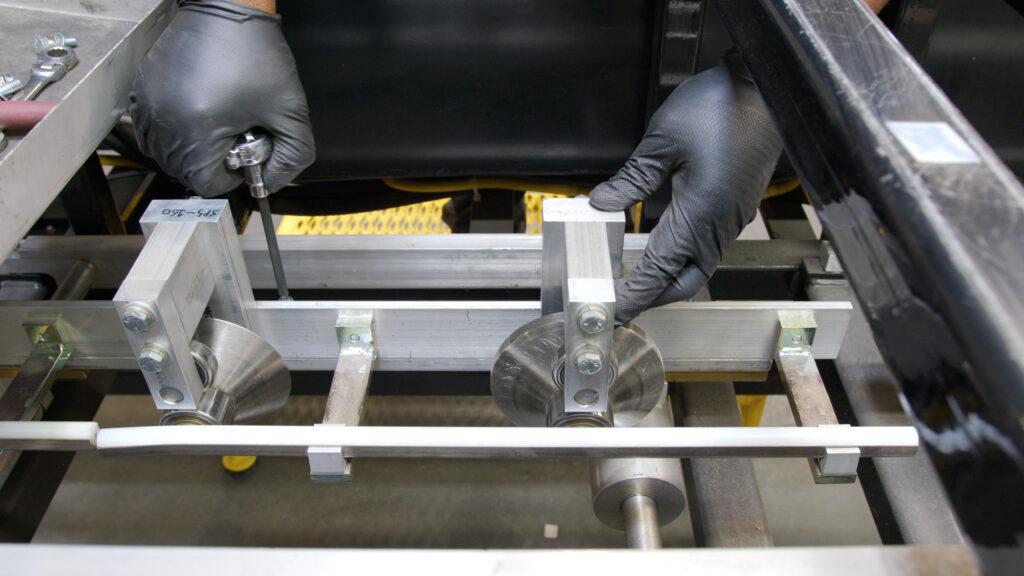
Problem 2: Overhead Expandable Arbor vs. Coil Stand
The expandable arbor is attached above the rollformer. Dual overhead expandable arbors can hold two coils for a combined load of 6,000 lbs. On the other hand, the coil stand sits external to the machine at the entry end so that the coil can feed into the rollformer from the coil stand. The stand can hold one coil.
Some contractors prefer a coil stand, especially if they’re using the rollformer as an in-plant machine, rather than transporting it to job sites. One fear some machine owners have with the overhead arbor is that workers may accidentally drop one into the machine while loading it, causing damage.
It’s fair to say this has happened before, although in extremely rare cases. Usually, this is due to carelessness on behalf of the forklift operator. However, with NTM machines, you can opt for the single free-standing de-coiler instead of the overhead coil reels. The overhead on the NTM is not required; most people prefer it as it makes the machine more compact for transportation. Plus, the dual overhead reel rack can hold two expandable arbors, making it easy to switch from one to the other without reloading the stand or hauling around multiple stands and coils. Now, let’s talk about maintaining chains in the drive system.
Problem 3: Chain System Issues
Another concern has to do with the drive roller chains stretching out. The fact is you must tighten any chain from time to time. This goes for motorcycles, scooters, snowmobiles, wind turbines, and anything else that uses a chain drive system. The machines need proper care, which means lubricating them a minimum of every 40 hours of operation and as needed, tightening them. Most rollformers use chains with their drive systems, so NTM is not unique in this. Lastly, we’ll dive into two types of profile forming rollers.
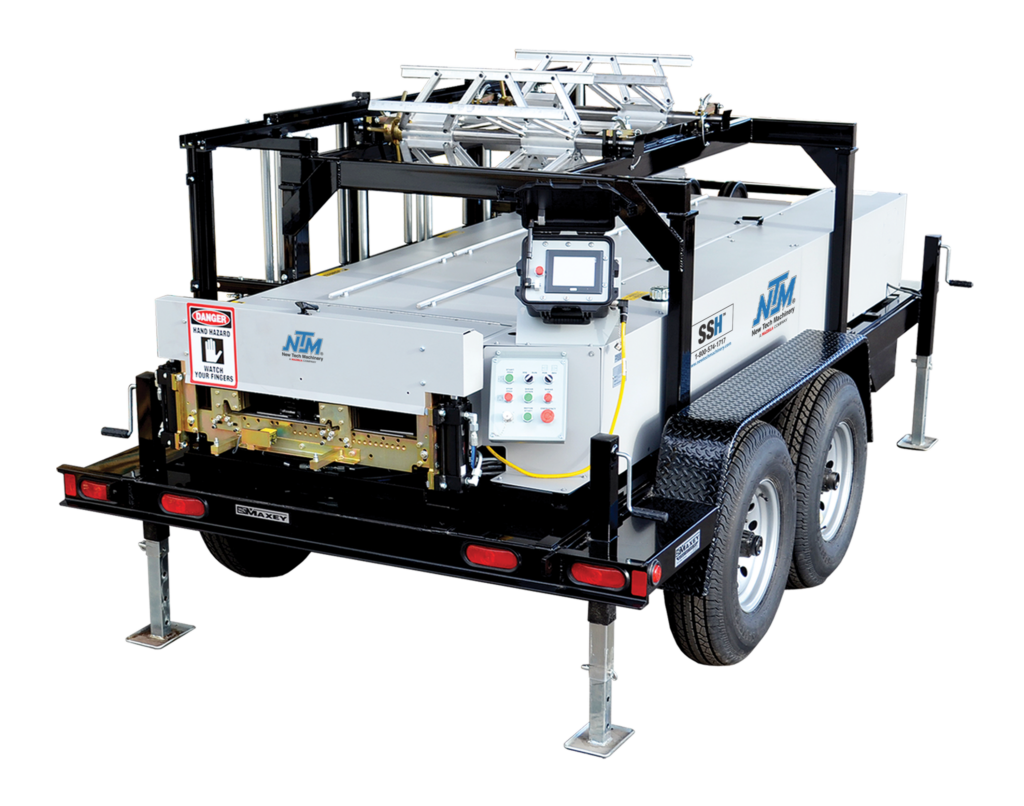
Problem 4: Profile Changeover vs. Cassettes
Machine operators can easily switch to another profile just by flipping the cassette in some rollforming machines. The tooling is mounted to the cassette, usually one profile on each side, so that is an advantage in saving time. However, to switch to another set of profiles on a cassette, you need a forklift.
With an NTM rollformer, like the SSQ II MultiPro Roof and Wall Panel Machine, you have 16 profiles to choose from, and it only takes 45 minutes to do a changeover. One person can do it with a wrench, so there’s no need for a forklift. If you’re changing profiles for different jobs, it’s not difficult to switch the tooling out in the field or in the plant. Plus, it’s much easier to make adjustments with the NTM profiles, and typically, much less material is required to dial them in properly. Because cassettes are covered, you can only shim the front forming rollers.
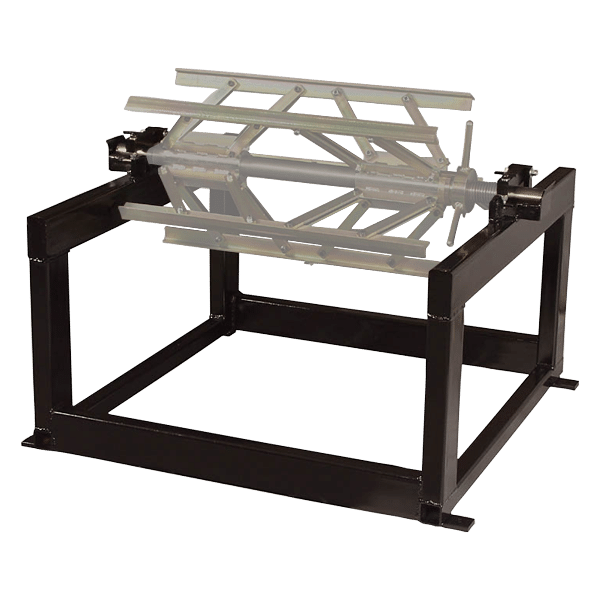
Will I Have Problems with an NTM Machine?
At NTM, we listen and respond to customer feedback. Due to recent customer requests, we’ve changed the covers on our SSQ II MultiPro machines to powder-coated aluminum to reduce glare and keep the outside of the machine cooler. We’ve also developed our new board & batten profile based on requests from contractors who saw the demand for it.
However, some concerns we commonly hear about NTM machines are based on misconceptions. To ensure that our machines are delivered ready to start working, it’s part of our manufacturing process to inspect each machine thoroughly, testing it for deficiencies before shipping it out. Like our users, we expect NTM machines to perform well under a variety of conditions and be the performance workhorse contractors can depend on.
If you’d like to learn more about NTM MultiPro Machines, our WAV Wall Panel Machine, or our Mach II Gutter Machines, contact one of our specialists.
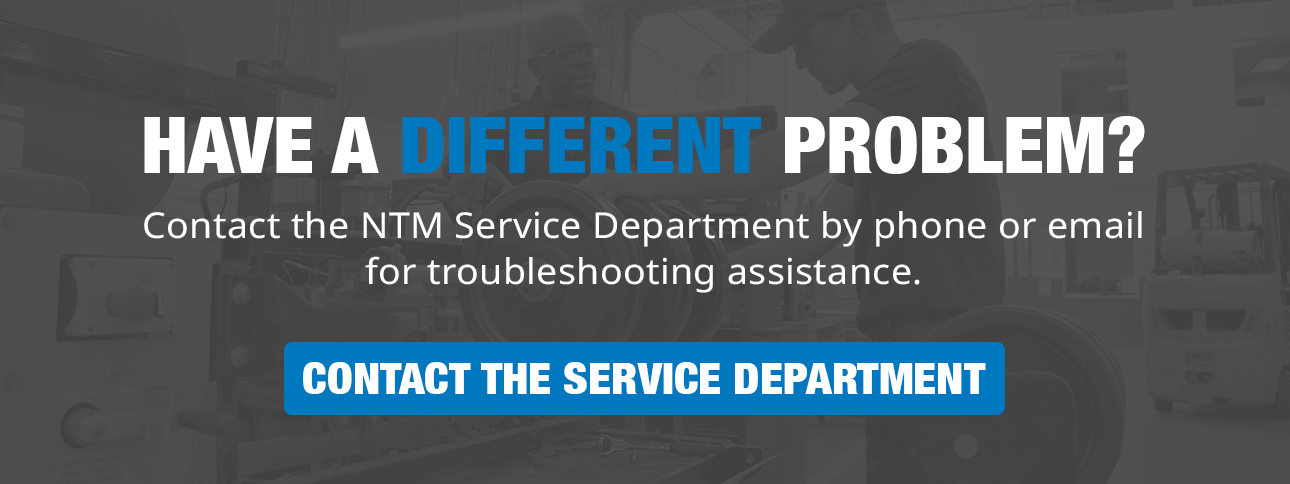