Common Problems with NTM Portable Rollforming Machines (and How to Solve Them)
What common problems do machine operators face with New Tech Machinery (NTM) portable rollformers, and how can they fix or prevent them in the first place?
Imagine you’re stuck out on some remote job site far away from your shop, and your panels or seamless gutters are running out crooked or marred by scratches. Installers are waiting, the contractor is feeling the strain of the delay, and you’re left to monkey around with adjustments.
Two things can save you: Preparation and knowledge. Having the right training, running test panels before you go, and knowing how to make proper adjustments from the manual or service content can save time and money, and possibly keep you from making a bad situation worse.
This article will drill down into problems you may have with your portable rollformer and how to prevent or solve them. We recommend sharing it with your team and saving it as a handy reference guide.
Operator tip: Download your machine’s manual onto your portable device for easy reference.
For over 30 years, New Tech Machinery (NTM) portable rollformers have been the go-to workhorses for contractors across the country. These machines fabricate high-quality panels and seamless gutters on-site, from high-country mountain jobs to beachfront Florida projects.
However, like all machinery, they can face various issues that impact production quality and efficiency. This comprehensive article outlines the most common problems contractors encounter with NTM rollformers—plus actionable tips to help you prevent or solve them quickly. Whether you’re new to rollforming or a seasoned pro, these tips will help you maximize machine performance, reduce downtime, and maintain high-quality output.
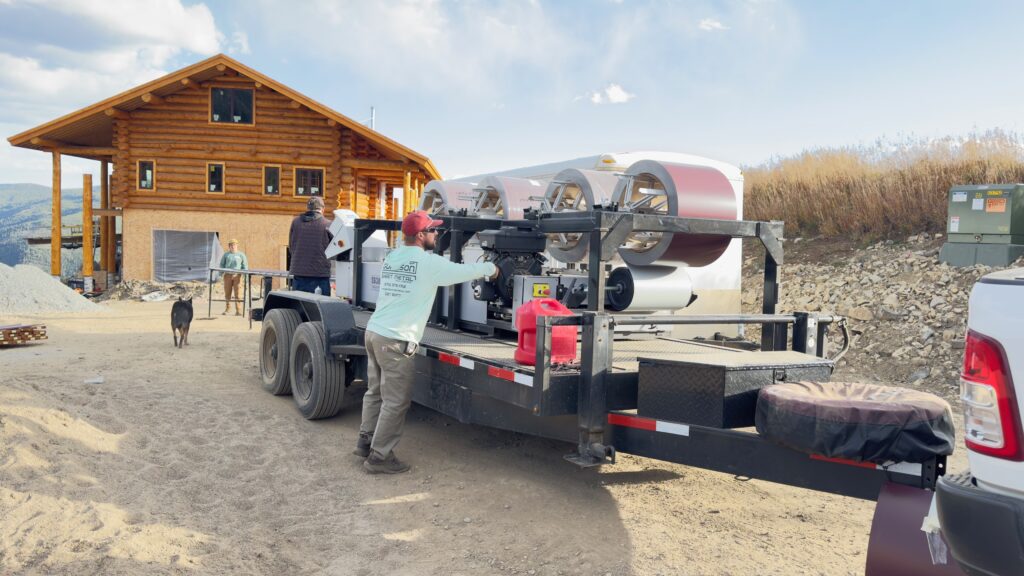
Table of Contents
- Introduction: Keeping Your Rollformer Humming
- Maintenance Neglect and Mechanical Issues
- Machine Setup and Alignment Errors
- Panel and Gutter Quality Problems
- Shear and Cutting Troubles
- User Errors and Training Gaps
- Support, Service, and Warranty Considerations
- A Breakdown of Best Practices
Introduction: Keep Your NTM Rollformer Humming: Maintenance Tips That Save You Time and Money
Chances are, your portable rollformer is the backbone of your operation. You’re benefiting from the ROI as long as it’s running smoothly. “It’s a money-printing machine,” one NTM customer remarked. But if something goes wrong?
NTM machines have earned their reputation for toughness and reliability. They’ll follow you from jobsite to jobsite, fabricating perfect panels or seamless gutters. But even they need care.
The truth is, most rollformer headaches aren’t random bad luck—they’re preventable. Delays and material waste often come down to skipping basic maintenance or setup steps that only take minutes but save hours of downtime.
Most common problems boil down to three simple areas: proper alignment, regular lubrication, and correct operation. Nail these basics, and you’ll not only extend your machine’s life but also keep production flowing without interruption.
Below, we’ll walk through the common problems that plague most operators and the simple fixes that will keep you rollforming instead of troubleshooting. These are practical, real-world solutions from machine operators who’ve called into our service department over issues that often could have been avoided.
Maintenance Neglect and Mechanical Issues
Maintenance is one of the primary factors that directly affects performance, output quality, and the long-term reliability of your rollforming equipment. Many service calls and repairs often stem from minor neglect—like skipping lubrication, failing to clean rollers, or forgetting to remove metal shavings that accumulate after a job.
Common Rollformer Maintenance Issues
• Dirty Drive Rollers and Forming Rollers
Dirt, debris, and metal shavings can build up on the rollers, causing black streaks, scuff marks on the material, and potential damage to the paint finish. When rollers are dirty, you might also notice slipping or misfeeds. Regularly wipe down and inspect the rollers, ensuring they’re free of any buildup. Avoid using harsh solvents that could damage polyurethane rollers.
• Lack of Lubrication (Chains, Shear, Bearings)
Rollforming machines rely on chains, shear blades, sprockets, and shafts that all require proper lubrication. Failing to lubricate these components can result in premature wear, slow operation, and even jammed mechanisms. Keep to a strict lubrication schedule as outlined in your machine’s manual—over-lubricating can attract debris, so use the recommended products and intervals.
• Loose or Worn Components
Vibration and heavy usage can cause bolts, nuts, and roller stations to loosen over time. If fasteners back out of alignment, the machine’s forming stations may shift, leading to poorly shaped gutters or panels. Conduct routine checks to ensure everything is properly tightened according to the manufacturer’s specifications.
• Hydraulic and Electrical Issues
For hydraulic-driven machines, low or dirty hydraulic fluid and damaged or dirty oil filters can cause erratic operation or poor cutting performance. On the electrical side, always keep an eye on fuses, wiring, and battery connections. When the machine’s components don’t receive consistent power or hydraulic pressure, you’ll often see inconsistent cuts or machine stalls.
Preventative Measures
• Follow the Manual’s Maintenance Schedule: Daily, weekly, monthly, and yearly tasks are all critical in preventing large-scale damage.
• Clean Regularly: Remove metal shavings, dust, and grease. A clean machine not only produces cleaner panels but also helps you spot worn parts early.
• Lubricate Appropriately: Adhere to the recommended products and intervals for chains, shear assemblies, and bearings. Avoid over-lubrication.
• Store Properly: When not in use, keep your machine in a dry, covered area. If it must stay outside, cover it and ensure moisture can’t build up.
Operator tip: Download the Complete Roof Panel & Gutter Machine Maintenance Schedule.
By making maintenance a priority, you’ll reduce the likelihood of breakdowns and improve the overall quality of your finished products.
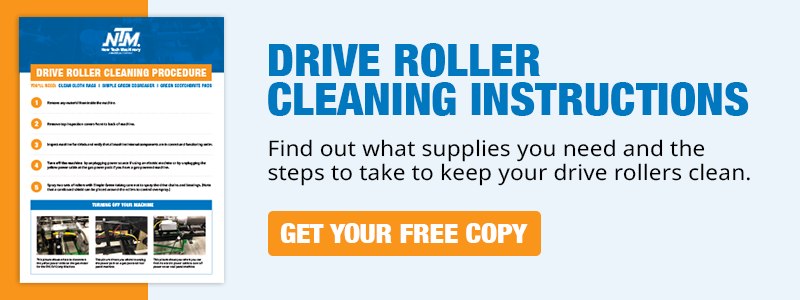
Machine Setup and Alignment Errors
Another common problem with portable rollformers is with the setup. Even the best-maintained rollformer can produce subpar results if not set up correctly. Alignment and calibration are critical, particularly because portable rollformers get moved around job sites, creating many opportunities for minor shifts that lead to major headaches.
Setup Mistakes and Consequences
• Skipping Test Runs
One of the easiest pitfalls is neglecting a test coil run before producing long panels. If you don’t verify alignment and coil specs upfront, you might end up wasting materials and scrambling for on-site fixes. Test run before you go.
• Improper Entry Guide Settings
The coil’s edges must match your machine’s entry guide. If the guides are too tight, the coil can buckle; too loose and it may slip, causing inconsistent forming or edge wave. Double-check your coil width with a tape measure—never assume it’s exactly what’s labeled.
• Coil Reel Misalignment
The decoiler or overhead reel should be precisely aligned with the machine’s feed path. A misaligned reel can lead to twisted or curved panels, while overly tight brake tension can stretch or scar the material.
• Unlevel Trailer or Run-Out Stands
Portable machines are often set up on trailers or uneven ground. If the machine isn’t level from side to side, panels can develop a curve (camber). Similarly, run-out stands that are too high or low can force the panel to bend as it exits.
• Wrong Tooling for the Profile
Multi-profile machines require specific roller sets and shear blades for each profile. Failing to swap the correct tooling or properly align the shear dies will cause jams and incorrect cuts.
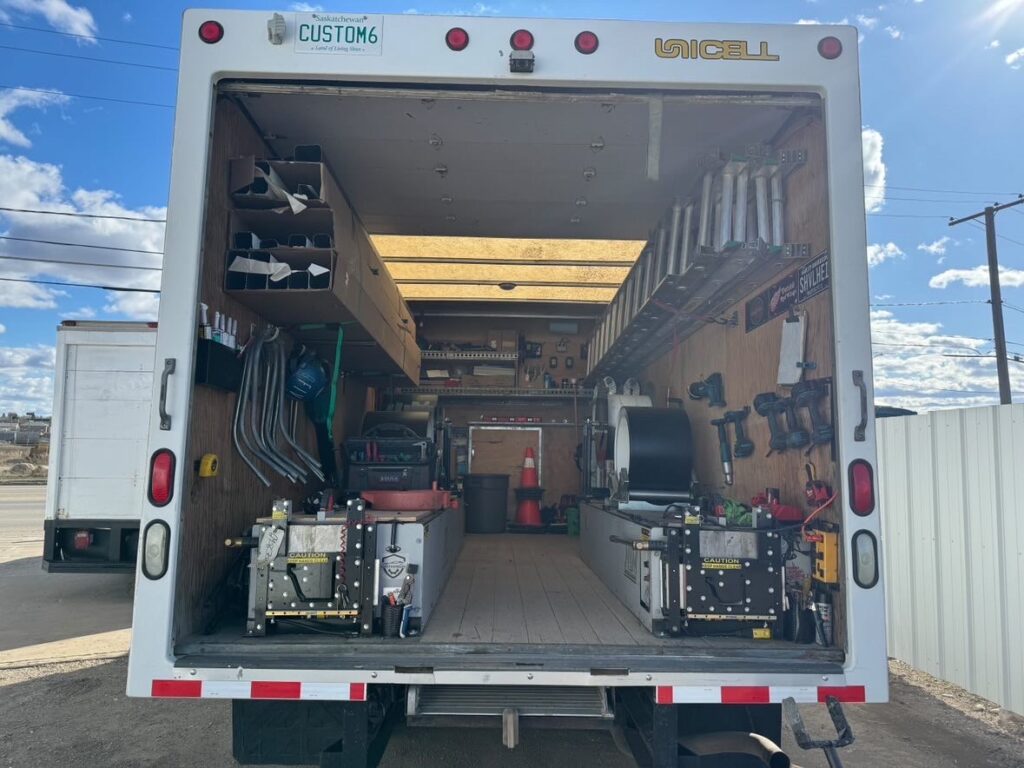
Best Practices for Setup
- Level the Machine
Use a carpenter’s level to ensure there’s no side-to-side tilt. Make small adjustments using jacks or blocks until it’s stable. - Align Reel & Guides
Position the coil reel or decoiler squarely behind the machine. Set the entry guides to match the exact coil width. - Run a Test Piece
Feed a short length of the actual coil to confirm straightness, profile correctness, and alignment. - Check Run-Out Supports
Stands should be at the same height as the exit point and aligned so the panel or gutter glides smoothly. - Confirm Tooling & Shear Setup
For multi-profile machines, ensure all profile-specific components—rollers, dies, blades—are properly installed and secured.
A thorough setup routine is essential to preventing issues like curved panels, edge waves, or jammed material. This initial prep time saves you far more time and money over the course of a project.
Panel and Gutter Quality Problems
Beyond mechanical hiccups, contractors may come across quality issues in the finished product. These include oil canning (waviness), scratches, incorrect dimensions, and curvature. Although some of these problems can stem from coil quality or installation errors, many are tied directly to how your machine is operated and maintained.
Oil Canning (Waviness)
• Description: Visibly wavy or slightly buckled flat areas on metal panels.
• Causes: Residual stress in coils, improper material handling, misaligned or overly tight rollers, poor tension-leveling at the mill, or a machine that’s not set up correctly.
• Prevention: Use quality, tension-leveled coil, maintain optimal roller alignment, and consider profiles with minor ribs or striations to reduce the appearance of waves.
Panel or Gutter Curvature
• Description: Panels or gutters that come out slightly curved (known as uphill or downhill).
• Causes: Unlevel trailers, misaligned run-out stands, or improper tension along the forming stations.
• Prevention and Fix: Level the machine, align support stands, and make small adjustments to any available camber control or straightening station if necessary.
Scratches and Marks on Material
• Description: Surface scratches, black streaks, or gouges on painted coil or gutters.
• Causes: Debris trapped in rollers, burrs on shear blades, or misalignment that drags the metal against the machine’s edges.
• Prevention: Keep the machine clean (especially the rollers and shear dies), store coil properly, and ensure there’s no leftover film or chips inside the machine. Check shear alignment for any sharp edges.
Incorrect Dimensions or Poor Fit
• Description: Panels or gutters with out-of-tolerance widths, profiles that don’t snap or lock properly, or gutter edges that misalign.
• Causes: Worn or misaligned tooling, skipped calibrations, or inconsistent coil dimensions.
• Prevention: Measure your coil carefully, verify tooling adjustments per the manual, and periodically test final output against specifications. If needed, recalibrate or replace worn parts.
Focusing on cleanliness, alignment, and correct coil selection will eliminate most panel and gutter quality issues at their source.
Shear and Cutting Troubles
The shear (or guillotine in gutter machines) is a critical component that directly affects productivity. When it functions perfectly, cut lengths are accurate, and edges are smooth. When it’s out of alignment, you’ll waste time, material, and possibly harm the machine. Most common problems with portable rollformer shears can be avoided or easily remedied.
Common Cutting Problems
• Misaligned Shear or Guillotine
If the blades don’t match the profile or the die is off-center, you’ll see diagonal cuts or experience jams when the blade pinches the metal. Always align the shear after changing profiles or replacing blades.
• Dull or Damaged Blades
Worn blades produce ragged cuts and can tear the material instead of shearing it. This issue is especially common for gutter machines cutting thicker or painted metals. Keep spares on hand for quick swaps.
• Jam at the Cut
A jam is often caused by a mis-timed cut or a foreign object stuck near the shear. Stop the machine immediately, clear any obstruction, and verify that the shear timing or sensor is working.
• Inaccurate Lengths
If you notice repeated undercut or overcut lengths, the encoder wheel or length calibration could be off. Clean the encoder wheel and recalibrate according to the machine’s guidelines.
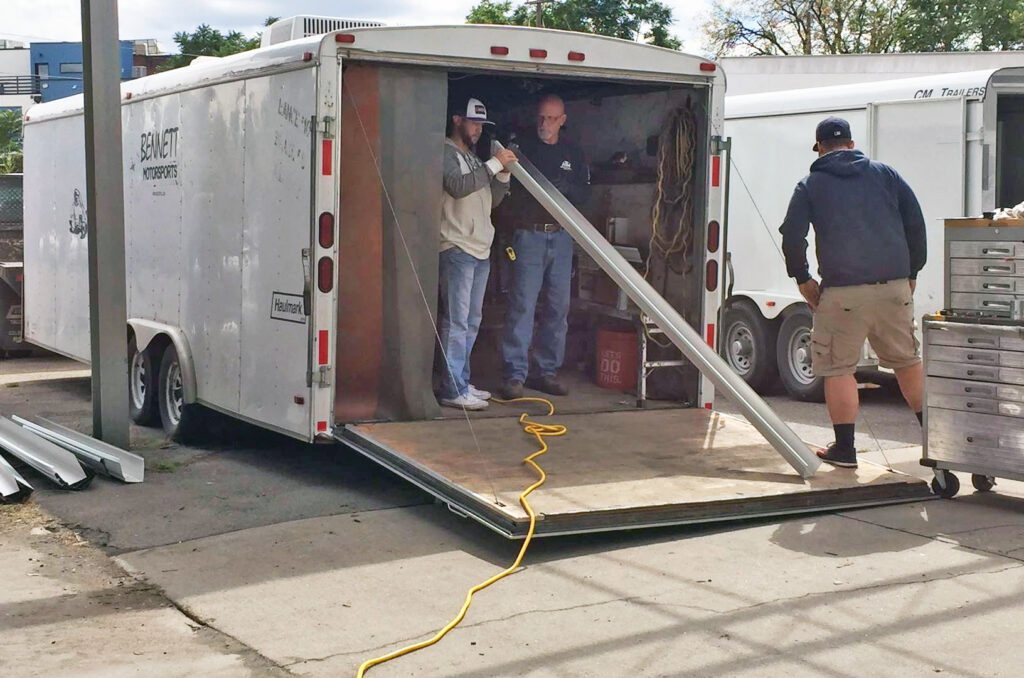
Shear Maintenance Tips
• Lubricate Regularly: Proper lubrication of shear blades prevents rust and reduces friction. Make sure the shear is kept lubricated every 30 to 50 cuts using Super Lube® Multi-Purpose Synthetic Grease (LUBE-GEL).
• Check Blade Clearance: Ensure upper and lower blades align perfectly and have minimal clearance.
• Inspect for Burrs or Nicks: Even a small burr can scratch the panel or cause binding. Sand them off or replace blades as needed.
• Perform Test Cuts: After any shear adjustment or blade change, make a few test cuts to confirm clean and accurate results.
Consistent attention to shear alignment and blade health guarantees efficient production and reduces wasted material.
User Errors and Training Gaps
Even a perfectly tuned, well-maintained machine can fail to produce quality work if the operator doesn’t follow correct procedures. User mistakes, often due to inadequate training, rank among the most common problems of rollforming machines. A rule of thumb–if you don’t know, don’t guess. Consult our Support page or contact our service team.
Frequent Operator-Related Issues
• Random Adjustments
Tweaking random bolts or calibration settings without understanding their impact can throw an entire forming station out of alignment. Avoid guesswork—always refer to the manual or consult with NTM’s service department.
• Feeding Improper Materials
Running metal outside the specified thickness or hardness can damage rollers, bearings, and even the frame. Using multiple pieces at once is also a recipe for jams and voids the warranty.
• Skipping Coil Setup Steps
Simple tasks like verifying coil width, setting entry guides, and leveling the machine can be overlooked in a rush. This typically results in waves, curvature, or alignment problems.
• Insufficient Training
Many contractors skip formal training due to time constraints, missing out on crucial techniques. Without adequate knowledge, operators are more likely to misalign rollers, use the wrong lubrication schedule, or ignore vital safety steps.
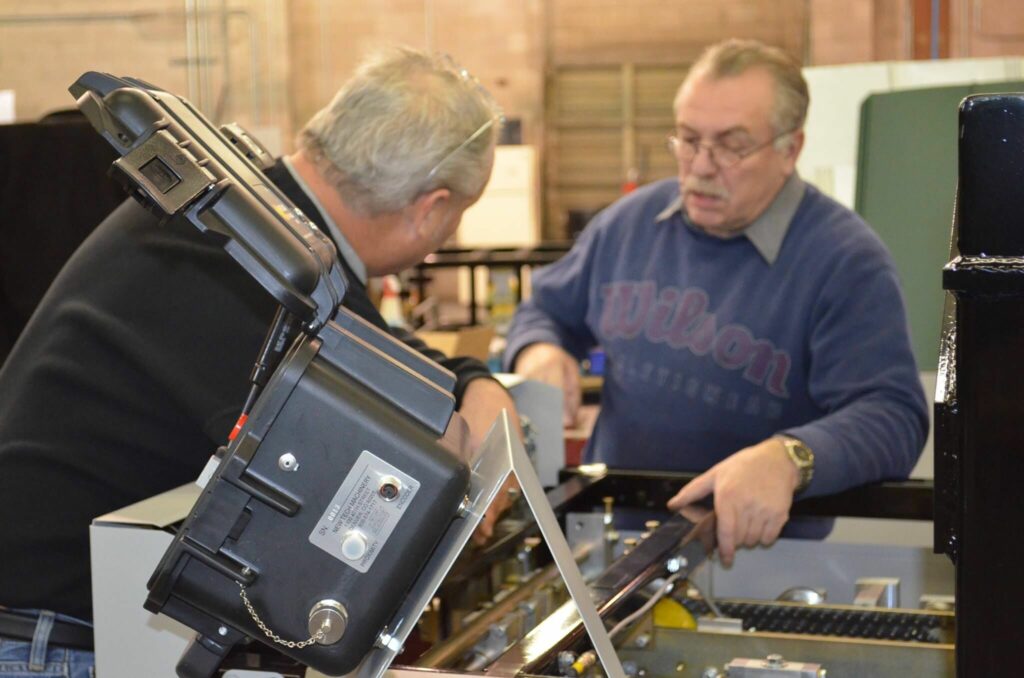
Training and Best Practices
• Take Advantage of Manufacturer Training: New Tech Machinery provides training resources, including online video tutorials, articles, and downloadable materials. NTM training is free to new machine owners at our facility in Aurora, Colorado. We encourage you to bring your whole crew. If you require training at your facility, or want additional training, schedule it with our Service Department. While this type of training isn’t free, it can save you money and problems in the long run.
• Develop an Onboarding Process: New hires should learn everything from coil loading and alignment to cleaning, lubrication, and safe machine operation.
• Encourage Manual Reviews: The user manual contains troubleshooting charts and step-by-step guides for most tasks. Keep a copy handy (in print or digital form) and ensure all operators know how to reference it.
• Foster a Culture of Inquiry: If the machine produces unusual results, operators should stop and investigate rather than keep running bad panels. Early detection is cheaper than a full batch of scrap.
With the right knowledge and habits, many user-induced issues become easily avoidable, ultimately boosting efficiency and product quality.
Support, Service, and Warranty Considerations
No matter how meticulously you care for your rollformer, problems can arise that require professional help. Knowing how to access support, what your warranty covers, and which parts to keep on hand can streamline any necessary repair process.
NTM Technical Support
• Remote Troubleshooting: Most issues can be resolved via phone or email. When calling our service department, make sure to have your machine model and serial number on-hand. Be ready to provide details about the issue as well as photos or videos showing the problem. The more information you can provide up front, the sooner your issue can be diagnosed and resolved.
• On-Site vs. In-House Service: If remote support isn’t enough, you can either send your machine to NTM for repair or request a technician visit your location. Keep in mind travel fees and scheduling availability.
• Parts Availability: NTM ships replacement parts to owners, often with expedited options.
Warranty Coverage
• Basic Terms: NTM machines typically come with a limited warranty covering parts and labor for a set number of years. Be sure to register your machine and review the warranty specifics.
• Coverage Limits: Using the machine outside its intended parameters or skipping routine maintenance can void your warranty.
• Process for Claims: Contact NTM with your serial number and evidence of the issue. You may need to ship faulty parts back for inspection.
Additional Resources
• NTM Learning Center: Offers articles, videos, and step-by-step guides for maintenance, troubleshooting, and machine operation.
• Distributors: If you purchased your machine through a distributor, they may also provide local support and training sessions.
Effective use of manufacturer support and adherence to warranty requirements will expedite repairs and help you maintain confidence in your equipment.
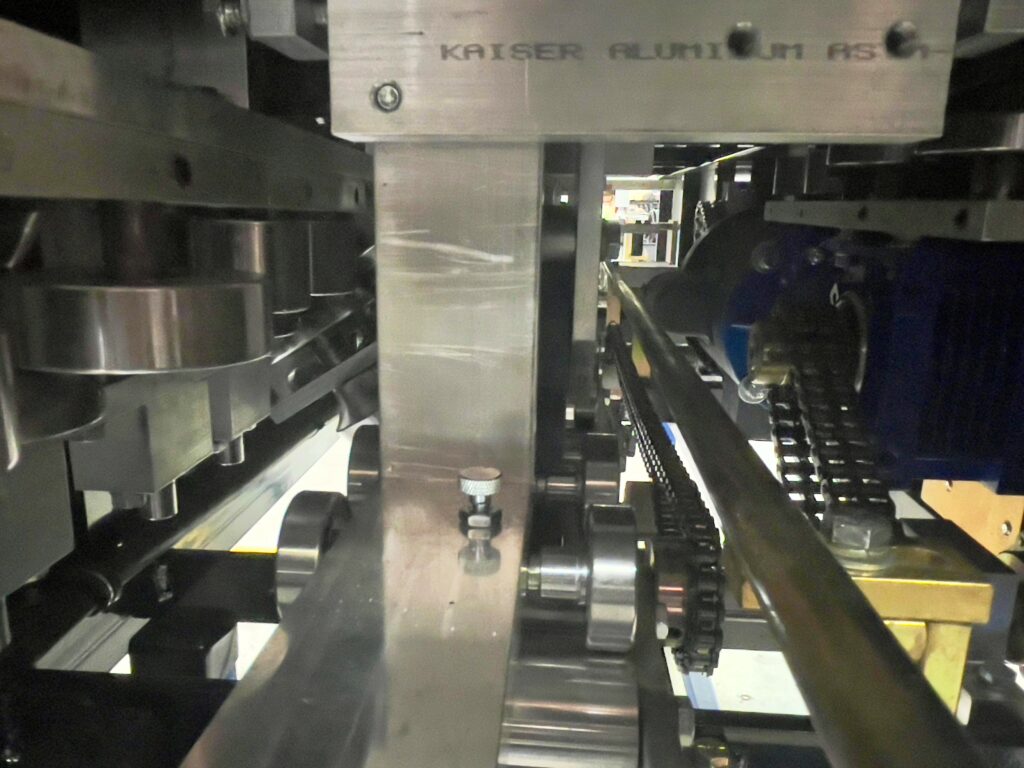
A Breakdown of Best Practices
Operating a New Tech Machinery portable rollforming machine comes with numerous advantages—on-site production, quick turnaround times, and the ability to customize panels or gutters. However, reaching this potential requires understanding the key pitfalls and solutions outlined in this guide:
- Make Maintenance Routine
Schedule and perform consistent inspections, cleanings, and lubrication. Small daily or weekly tasks save massive repair costs down the line. - Master the Setup
Level your machine, align the coil properly, run test pieces, and confirm the correct profile or tooling before ramping up production. - Use Proper Materials
Feed only the coil types and thicknesses recommended. Substandard or off-spec metals can cause forming inconsistencies or damage components. - Keep it Clean
Avoid debris buildup on rollers, shear blades, and forming stations. Cleanliness directly affects product appearance and machine longevity. - Train Your Team
Formal training—whether from NTM or in-house experts—prevents errors that waste materials and time. Encourage all operators to reference the manual and ask questions.
Operator tip: Download the Drive Roller Cleaning Procedure.
Keep your rollforming operation running smoothly by following these basics: maintain your machine regularly, set it up right every time, and make sure your crew knows what they’re doing. This simple approach means fewer job site issues, better panels, and a machine that’ll keep making you money for years. Your bottom line will thank you.
For information about NTM portable metal roof and wall panel or gutter machines, contact us. One of our knowlegeable account managers will be happy to help out.
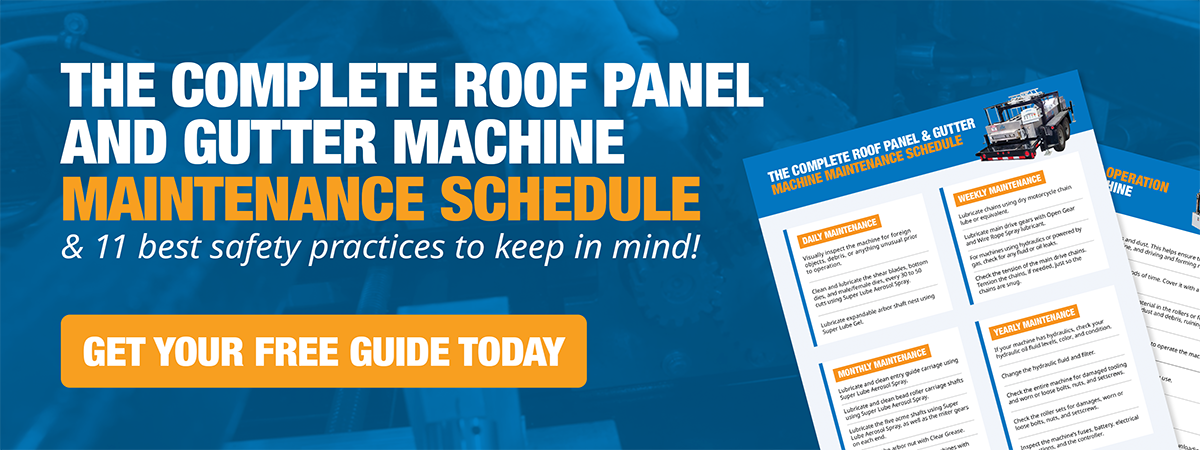